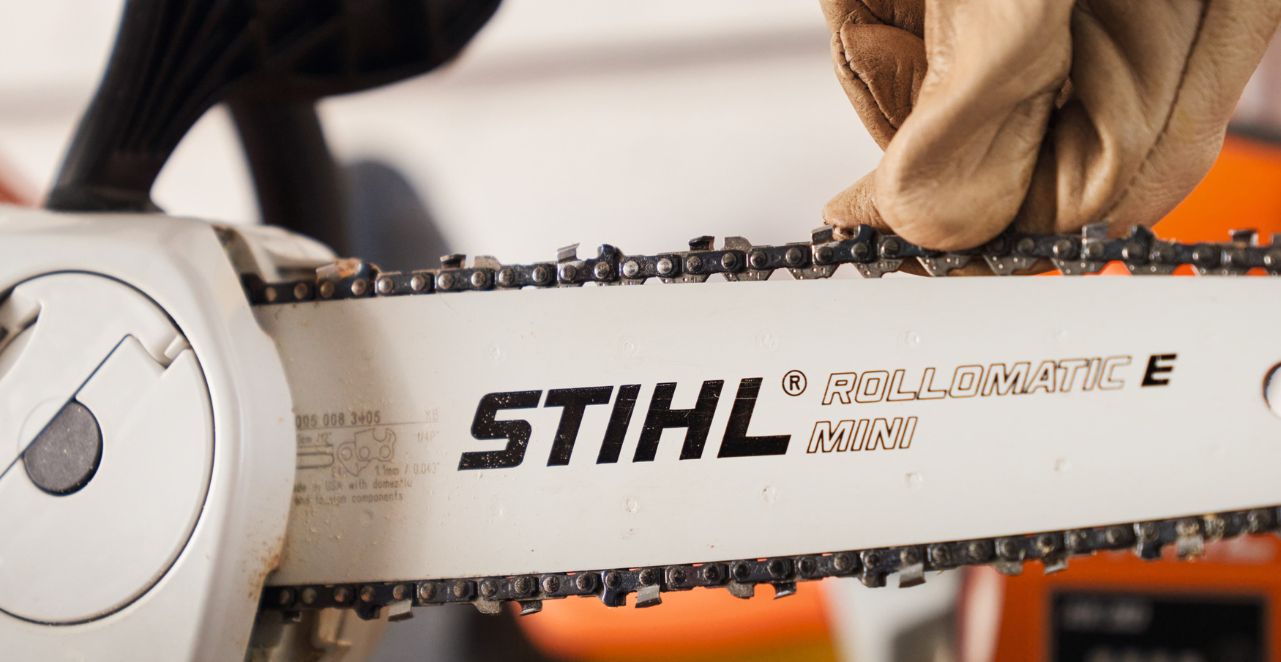
#Products
STIHL Chainsaw Chain: Engineered to Perform
Look closely at your STIHL chainsaw chain and you may spot some clever details that might usually go unnoticed. Since 1974, all STIHL chainsaw chain has been precision engineered at our dedicated STIHL owned plants in Switzerland, close to the border of southern Germany. Due to constantly growing demand, facilities have steadily expanded over the past few years and the plant now employs around 850 staff, exporting to 160 countries across the globe.
Every cutting tooth in each STIHL chainsaw chain loop is individually inspected and put through a quality control test, so that the highest levels of quality are always met. Learn more about the engineering choices and manufacturing processes that makes STIHL chainsaw chains a cut above the rest.
How Does a STIHL Chainsaw Chain Work?
All STIHL chainsaw chain works the same way; as it passes through a log, each tooth planes a chip from the wood. In this process the top plate cutting edge (1) lifts the chip from the wood while the side plate cutting edge (2) separates the chip from the wood in the cut.
The depth gauge (5) determines the height at which the cutter enters the wood and the thickness of the chip removed. The depth gauge setting is the small distance between the top edge of the depth gauge (3) and the front edge of the top plate (4). In most cases the depth gauge setting is 0.65mm, but this can vary to 0.80mm or 0.45mm depending on the chain pitch. To achieve optimum chain running behaviour (smooth cutting and lower likelihood of kickback) the depth gauge must slope upward (5) over its entirety, in line with the wear marker (6).
Each tooth is made from special hardened steel, then the top plate (4) and side plate (7) are galvanized with a chromium coating for additional resistance against wear, meaning they stay sharper for longer. The top plate (4) and side plate (7) taper to the rear to form a clearance angle, meaning the cutter does not jam in the wood. This clearance angle is .L/’;/retained even when the cutter is sharpened. Filing the depth gauge using a sharpening aid means the ideal depth gauge setting of 0.65mm is always maintained.
Oilomatic: Keeping the Chain Cool
The Oilomatic lubricating system used in STIHL chainsaw chains reduces friction and wear by directing the chain oil to where it’s needed the most. A fine oil channel in each drive link (3 on the image below) picks up oil from the inlet hole in the bar groove (1) and delivers it quickly and evenly to the chain rivets and running surfaces of the teeth. STIHL Oilomatic chains also feature an oil reservoir (4) in addition to the oil channels. The reservoir takes the form of a bore in each drive link and improves chain lubrication by providing additional oil around the bar nose and on the underside of the chainsaw bar. This improvement is particularly beneficial when cross cutting from above, as in this case, the oil is needed most on the underside of the guide bar.
The Oilomatic system results in considerably reduced wear and better flexibility of the chain, prolonging the chain’s life, as well as that of the guide bar and sprocket too. What’s more, an Oilomatic chainsaw chain consumes no more oil than other chains. The oil is simply better distributed and used more efficiently.
Other Production Processes
Other elements of the manufacturing process make a lasting impression on the lifespan of each chain. Every rivet in a STIHL chainsaw chain is induction hardened. This process heats the rivets through electromagnetic induction, followed by quenching to alter the structure of the outer metal to make it harder. This results in a rivet that is more resistant to wear.
Secondly, a specially adapted stamping technique is used to create mirror smooth joint borings on the teeth and tie straps, improving the running properties of the chain and again increasing the service life.
The final production step of every STIHL chain is pre-stretching. The chain is exposed to a high and constant tensile load before being packaged, helping to keep stretching to a minimum during the chain’s first use.
The latest chainsaw chain development
It’s not often developments in chainsaw chain technology cause a stir, but STIHL Rapid Hexa is fully deserving of the attention it’s gained around the world. Consisting of a patented ‘V’ shaped cutting tooth and hexagonal file, Hexa offers professional forestry chainsaw users a 10% boost in cutting performance and a much enhanced sharpening experience unlike anything else on the market.
the top plate kerf of each cutting tooth is narrower than the equivalent Rapid Super chain, leading to an improvement in cutting speed and efficiency. A second optimisation is the 25° sharpening angle. Testing has found that a slightly reduced angle performs better in diagonal felling cuts, which is ideal for arborists and tree surgeons alike.
Finally, the most striking update to the chain is the 60°, V shaped side plate angle. The hexagonal file sits perfectly in the tooth’s profile, leading to simplified and faster sharpening. With Rapid Hexa it’s easy to achieve a high-quality cutting edge, and due to the less acute angle of the leading cutting corner the tooth is less prone to wear and therefore stays sharper for longer.
Learn more about STIHL’s new Rapid Hexa Chain here.